Editor’s note: This article is the first in a series of mini-articles that outline the benefits and the value proposition available by Salamander heaters. This article is an introduction to Salamander Heaters.
Document also available for download (pdf) here.
Salamander Solutions is bringing advanced heater technology to bear on oil field challenges to improve profitability of difficult hydrocarbons. Salamander was spun off from Shell in mid-2017 with Shell remaining as a minority owner.
Salamander has deep roots in the advanced heavy oil technology group within the Shell Organization. The management team includes many of the developers and patent holders of Shell’s In situ Upgrading/In situ Conversion Process (IUP/ICP) technology initially intended for the vast oil shale and heavy oil resources. Shell tested the technology for more than 15 years in their labs, in numerical simulations, at bench top scale, and ultimately in several field pilots in three countries culminating in the Viking pilot that produced 200,000 bbls of 30oAPI oil from 8oAPI in situ oil at Shell’s Peace River field (now owned by CNRL).
Although the economics of ICP/IUP do not work at today’s $50 – $60 prices, the key enabling technology developed for ICP/IUP, namely a very long, rugged, high power electric heater has emerged as a clear technology success story. Many “conventional” applications of the heater have been identified including:
- Improve production from Cold Producers (including CHOPS wells)
- Accelerate production and increase performance from SAGD well Pairs
- Reduce operating cost and improve uptime of Waxy Oil wells
- Provide unprecedented reliability for Deepwater flowlines simplifying field layout and reducing cost of flow assurance
The process of downhole heating of cold-production wells is simple and the opportunities are robust at today’s prices, adding incremental barrels at $10 – $15/bbl with payouts of 1.0 to 1.5 years. Deepwater applications can result in simplified field layouts significantly lowering field development costs. The goal of the Salamander team is to commercialize the technology, bringing benefits to heavy oil and deepwater fields around the globe.
Salamander Heaters – Developed by Shell
The initial design conditions for ICP/IUP were challenging: 650oC heater skin temperatures, 1200 W/m heater delivery, heater lengths up to 1100 m with a service life of up to 6-8 years. This combination of conditions had never been achieved by the industry and the difficulty of the challenge required 15 years to achieve the breakthrough results.
The new applications for a Salamander heater will not be nearly as strenuous. A typical application will require 300oC and 400 W/m heat delivery. By designing to higher specification than needed, Salamander heaters have an inherent design margin enabling longer lengths (up to 2000 m) and a longer service life (up to 10 years or more).
Salamander heaters are the only heaters capable of delivering high power at extreme lengths. This is made possible by our patented manufacturing process that has eliminated splices, which are traditional failure points and barriers to deployment. Although our heaters are ready for commercial deployment in their present configuration, we have a clear path to reduce costs by an additional 30%.
By studying the failure modes for more than five years, Shell scientists, engineers, and technicians were able to make break-through performance improvements compared to the heaters offered by the competition. The result is a simple design that performs to much higher voltages than other heater cables in the market. Higher voltages allow higher power (or smaller sizes and thus lower cost) enabling a greater flexibility in applications.
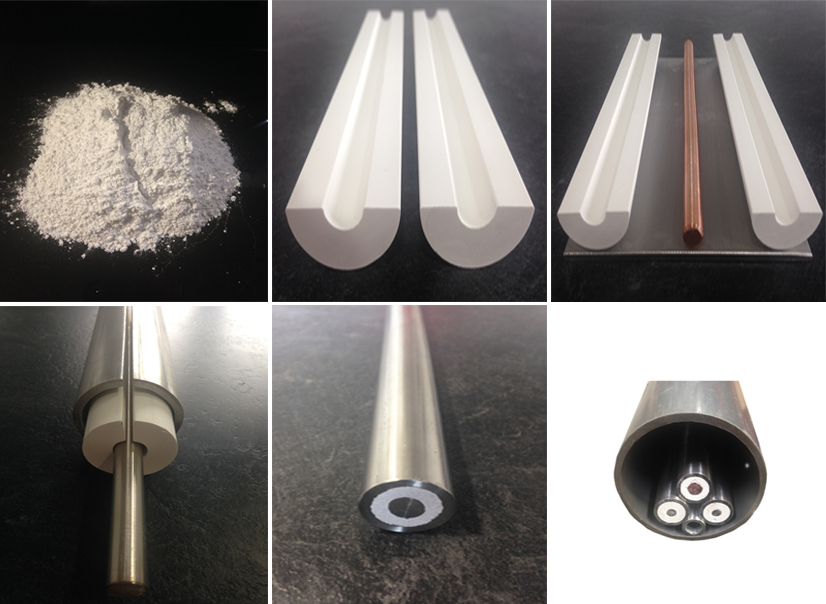
Figure 1 – Steps in the fabrication process for Salamander heaters are shown above. Magnesium oxide powder (electrical insulation material) is formed into grooved blocks. The central electrical conductor rod is added. The outer stainless-steel sheath is formed around the blocks to provide corrosion resistance. The assembly is drawn to the final length. Multiple conductors and instrumentation tube are pulled into carrier pipe, ready to be assembled on a reel and shipped to the site.
Salamander Heaters – Unmatched in Marketplace
Salamander heaters are designed and customized for the particular application. For “cold” heavy oil well producers, a typical Salamander heater would include a heated length of 1,000 – 2,000 m and a heat injection rate of about 500 W/m. For a IUP/ICP applications, similar heated lengths could deliver 1200 W/m. For subsea applications, the much lower heat requirement (only about 50 W/m) enables Salamander heater to reach lengths of 10 km or more. In every case, these lengths are achieved without splices, which have proven to be both failure points and impediments to the installation inside wellbores noted for their tight clearances. The ability to deliver power in these configurations has never before been possible in the industry. Salamander is gearing up to deploy this new capability in the industry to increase production and/or solve challenging flow problems to enable greater profitability for our customers.
Next Month: Salamander BoostWell™ Application to improve production from “cold” heavy oil wells will be featured.